Analysis of Factors Affecting Drying Rate of Vacuum Freeze Dryer
- Share
- publisher
- Steve
- Issue Time
- Sep 30,2021
Summary
The freeze-drying process is a complex heat and mass transfer process, involving refrigeration, vacuum, electronics, chemistry, cryogenic medicine and other disciplines, with high technical content and complex freeze drying processes. In the traditional Chinese medicine, food and other industries, the vacuum freeze dryer is one of the most popular equipment.
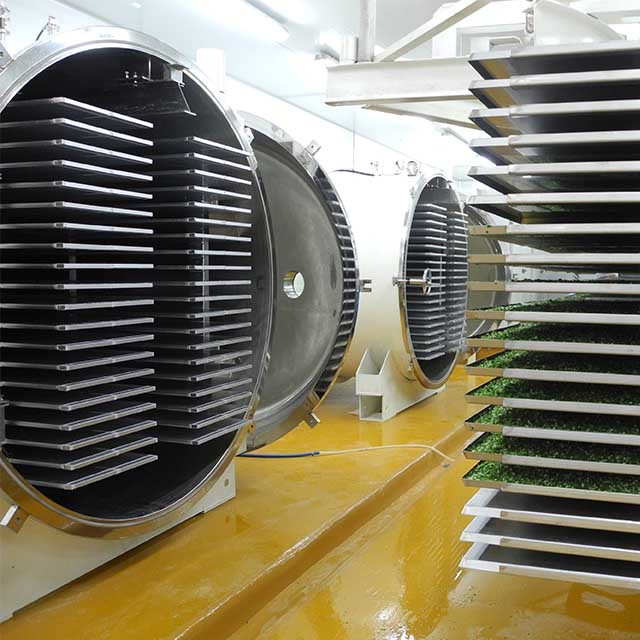
The freeze-drying process is a complex heat and mass transfer process, involving refrigeration, vacuum, electronics, chemistry, cryogenic medicine and other disciplines, with high technical content and complex freeze drying processes. In the traditional Chinese medicine, food and other industries, the vacuum freeze dryer is one of the most popular equipment.
From the structural point of view, the vacuum freeze dryer is a combination of refrigeration system, vacuum system, heat recirculation system, and drying system, thereby introducing a new type of cabinet, which can make more efficient use of the material storage space in the cabinet. Perform freeze vacuum drying. At present, the vacuum freeze dryer is suitable for drying various materials such as raw materials, Chinese herbal medicines, pharmaceutical intermediates, and food.
According to the industry, when the vacuum freeze dryer is working, the drying rate is a point of great concern to users. However, in actual operation, it is often found that the drying rate is not satisfactory. So, what are the factors that affect the drying rate of the vacuum freeze dryer?
Material pre-freezing rate
It is understood that the pre-freezing of materials is the first thing the freeze dryer needs to do when it is working. Pre-freezing can be divided into quick freezing and slow freezing. The size of crystals formed during freezing greatly affects the overall drying rate and the dissolution rate of the dried product.
Specifically, the process of quick freezing and slow freezing has the following differences: the ice crystals produced by quick freezing are smaller, and the ice crystals produced by slow freezing are larger. Large ice crystals are conducive to sublimation, while small ice crystals are not conducive to sublimation. Fast freezing leads to low sublimation rate and fast desorption rate; slow freezing leads to fast sublimation rate and slow resolution rate.
Therefore, the industry pointed out that the speed of pre-freezing must be accurately grasped according to the materials.
The pressure in the freeze drying chamber
According to the industry, the pressure in the drying chamber will directly affect the rate of heat and mass transfer (water vapor). Among them, in terms of mass transfer, the lower the pressure, the better, and for heat transfer, the higher the pressure, the better.
Since the mass transfer rate is mainly determined by the temperature and pressure of the sublimation interface and the surface of the drying layer, to increase the escape rate of water vapor in the drying layer, there are generally two operations: increase the temperature of the sublimation interface to make the interface water vapor The pressure increases. Or increase the vacuum of the drying chamber and reduce the vapor pressure on the surface of the drying layer.
Material form
It is reported that in the freeze drying process, the form of freeze dried materials is usually divided into solid and liquid. The bulk density of the solid and the component density of the liquid both affect the freezing time of the material.
Wet weight load
It is understood that when materials are lyophilized, there is a certain ratio of surface area to material thickness after being packed into containers. When drying, the dry wet weight load per unit area of the tray is an important factor in determining the drying time.
In general, the thinner the thickness of the material accumulation, the faster the heat and mass transfer speed, and the shorter the drying time. However, if the material is thin, there will be less material dried per batch per unit freeze-dried area, which will be disadvantageous to increase the unit freeze dried area and the output per unit time. Therefore, comprehensive considerations need to be made according to the materials.
At present, there are many kinds of vacuum freeze drying equipment on the market, and many times manufacturers have updated and upgraded their automatic control in order to improve the drying efficiency. Some equipment manufacturers said that the new type of freeze drying equipment has changed the tedious operation in the past drying process, prevented material pollution, and realized the automation of drying and sublimation. The relevant person in charge said, “This model has shelf heating and programmable functions, can memorize the freeze drying curve, and comes with a u-disk extraction function, which makes it easier to observe the freeze drying process of the material."