Comparison Of Advantages And Disadvantages Of Mixer
- Share
- publisher
- Steve
- Issue Time
- Oct 10,2020
Summary
Mixing is an indispensable production process in modern industry. With the continuous development of industry, the development of mixer will be more and more powerful. Mixer covers the entire industrial field, such as chemical industry, food, building materials, medicine, chemical fertilizer. There are many kinds of powder mixing equipment. The advantages and disadvantages of mechanical mixing equipment are analyzed below.
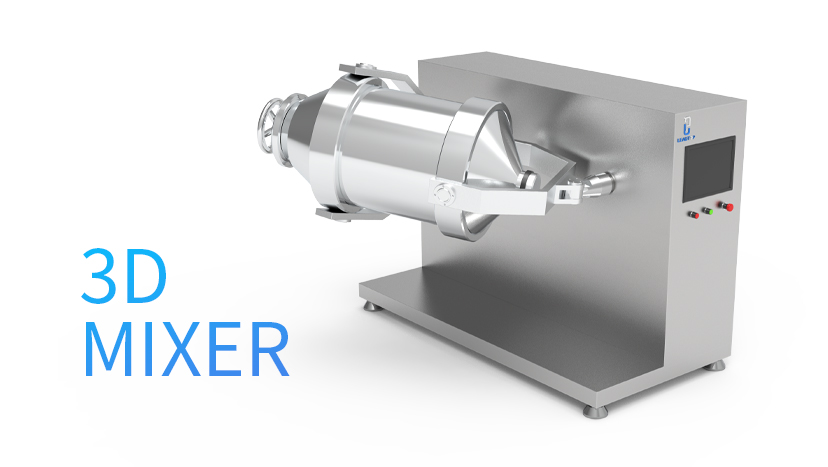
Mixing is an indispensable production process in modern industry. With the continuous development of industry, the development of mixer will be more and more powerful. Mixer covers the entire industrial field, such as chemical industry, food, building materials, medicine, chemical fertilizer. The products we use every day have at least one mixing process in production.
The use of mixer can make the material processing speed faster. For manufacturers, people hope to use a shorter time to complete the processing process, and the mixer can meet the needs of people. During the operation of the equipment, the materials can be processed at a high speed. After the completion of the equipment, the material texture is uniform, and there is no residue After the operation, the operators do not need to carry out too much finishing work.
There are many kinds of powder mixing equipment. The advantages and disadvantages of mechanical mixing equipment are analyzed below.
1. 3D mixer
The mixing principle of three-dimensional mixer is gravity convection diffusion mixing.
Advantage:
(1) The multi-dimensional space motion can make the material mix well.
(2) There is no centrifugal force in the mixing process.
(3) There is no dead corner in mixing.
Disadvantages:
(1) It is not easy to achieve fine mixing on the micro level.
(2) When the kinetic energy of the powder is too large, the light powder and fine powder are easy to float and not easy to mix into the main powder.
(3) Long mixing time, high power consumption and low loading rate.
(4) The equipment is not easy to be enlarged due to safety problems.
(5) It is not easy for the equipment to be larger than 1000 liters.
2. V mixer
The mixing principle of V-type mixer is gravity convection diffusion mixing.
Advantage:
(1) There is no dead corner in mixing.
(2) When the mixed powder has good fluidity and similar physical properties, better mixing effect can be obtained.
Disadvantages:
(1) It is difficult for the powder to mix well.
(2) Fine powder and light powder are not easy to mix into the main powder.
(3) There is gravity lifting movement, so the power consumption is high.
(4) If there is throwing and smashing, the shape of powder will be destroyed.
3. Double cone mixer
The mixing principle of double cone mixer is gravity convection diffusion mixing.
Advantage:
(1) The double cone cylinder can meet the requirements of no dead angle for mixture.
(2) Soft running speed will not damage fragile materials.
(3) It can meet the requirements of batch mixing in production.
Disadvantages:
(1) Fine mixing cannot be achieved.
(2) The mixing efficiency is low and the mixing time is long.
4. Horizontal screw belt mixer
The mixing principle of horizontal screw belt mixer is: forced shear mixing.
Advantage:
(1) Large loading factor and small equipment area.
(2) With the shear blade inside, the micro mixing can be achieved.
(3) According to the production demand, the equipment can be used as a large-scale machine, and the price is cheaper than other mixers.
Disadvantages:
(1) If the barrel is fixed, there will be a dead angle of material.
(2) The starting load of the equipment is very large, so it is difficult to start at full load, which consumes time and electricity.
(3) There is residue in the discharge.
5. Single cone double screw mixer
The mixing principle of single cone double screw mixer is: forced shear mixing.
Advantage:
(1) The structure is simple and can be used as a mainframe.
(2) It will not overheat heat sensitive materials.
(3) spray and heating can be added.
Disadvantages:
(1) The mixing time is long and the efficiency is low.
(2) The height of the equipment is too high. For the same mixing capacity, the height of double helix equipment is twice or even higher than other equipment.
(3) There is a dead angle at the bottom of the equipment, so it is necessary to discharge part of the material in the middle and mix the bottom material repeatedly to avoid the dead angle.
6. Square cone mixer
The mixing principle of square cone mixer is gravity convection diffusion mixing.
Advantage:
(1) It has the advantages of novel design, compact structure, beautiful appearance and general mixing effect.
(2) There is no dead angle in fine polishing and mixing.
(3) The hopper at the lower end of the square cone can be replaced as a storage bin for easy operation.
(4) It is easy to discharge and clean the barrel.
Disadvantages:
(1) Fine mixing cannot be achieved.
(2) Due to the limitation of equipment, it is not easy to enlarge.
(3) The equipment is complex and bulky, and its cost is high.