Rapid Mix Granulator – Operation and Cleaning Guide
- Share
- publisher
- Xavier
- Issue Time
- Nov 26,2019
Summary
A rapid mix granulator is a multi-purpose mixer/processor equally suitable for high speed dispersion of dry powders and their granulation with aqueous or organic solvents. The equipment is designed to achieve rapid mixing and the formation of consistent granules required for the production of high quality pharmaceutical tablets for solid dosage forms of medication. Good mixing and control of granule size leads to fast tableting speeds and high quality products with low rejection rate.
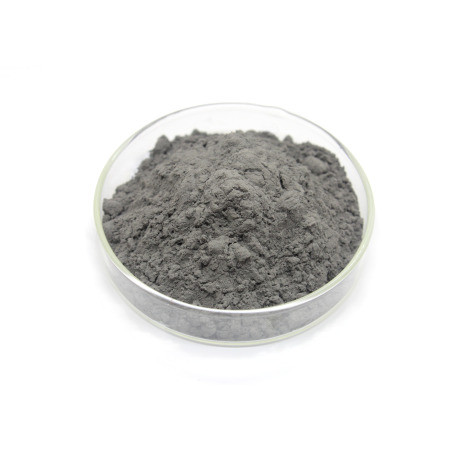
Rapid Mix Granulator – Operation and Cleaning Guide
Operating principle
A rapid mix granulator is a multi-purpose mixer/processor equally suitable for high speed dispersion of dry powders (including effervescent powders) and their granulation with aqueous or organic solvents. The equipment is designed to achieve rapid mixing and the formation of consistent granules required for the production of high quality pharmaceutical tablets for solid dosage forms of medication. Good mixing and control of granule size leads to fast tableting speeds and high quality products with low rejection rate.
A rapid mixer granulator usually comprises mixing bowl with a bottom entry agitator or impeller for mixing the materials and a side mounted chopper for granulating the mixture. The operating principle is based on agitation of the contents of the bowl at moderate speed and then running the blade of the chopper at high speeds to achieve granulation. Broadly the operating process therefore takes place in 3 steps
· Dry materials are mixed at high speed for typically 3 to 5minutes.
· The mixer is set at a slow speed and liquid binder is added to the dry materials. Mixing of the wet materials typically takes a further 5-10 minutes. The impeller breaks up the mass of material into smaller fragments or granules.
· Wet granulation is achieved by running the mixer at high speed and it typically takes another 5 to 10 minutes to produce granules of 0.5 to 1.5 mm average diameter. The actual granulation time depends on the nature of the starting materials (e.g., density and particle size), the binder, and the speed of the chopper. In this step it is the design and speed of the chopper that determines the uniformity and size of the produced granules. The chopper runs at high speed usually above 200 rpm, and typically between 1200 and 2000 rpm.
Operating procedure
A. Pre-start Up
1. Ensure that the processing area is clean.
2. Check that the correct materials have been selected for the granulation process.
3. Remove the “cleaned” label from the granulator after checking the information provided (especially previously used materials).
4. Place the equipment label on the machine.
B. Start Up and operation
· Use protective latex gloves when loading and unloading materials.
· Open the lid of the granulator and load the material to the bowl as per the sequence indicated in the Batch Manufacturing Record (BMR) or specification.
· Close the lid and secure the two locking clamps.
· Fix the dry mixing speed as specified in the BMR. Turn on the power and start the dry mixing process. Run for the specified mixing period.
· Slow the mixer impeller as specified in the BMR to the speed required for binder addition.
· Add the binder solution by supplying through the solution inlet port.
· Check the impeller speed is as per BMR and for the wet mixing process, and run for the required period.
· Increase the speed and set the chopper speed to that required for granulation. Check regularly to ensure that granulation is complete.
· Open the discharge gate and allow the wet mass to flow into a clean FBD bowl, located under the discharge port.
C. Shut Down
· Stop the chopper and impeller, and open the equipment top lid. Remove any remaining mix by scraping it from the sides of the bowl.
· Check that all materials are removed.
· Switch off the main power supply.
Cleaning Procedures
1. Cleaning during batch changeover, but with the same product
· Check that the equipment and area around the equipment is clean.
· Remove the “cleaned” label from the machine.
· Place the equipment “in use” label on the machine.
2. Cleaning during product changeover
· Check that the equipment and area around the equipment is clean and free from waste or materials from previous products.
· Check and review the “rinse water analysis report” and attach to the BMR.
· Remove the “cleaned” label from the machine.
· Check the relative humidity and room temperature, making sure to document it in the BMR log.
· If the temperature is not within the specified limit, inform the maintenance personnel and do not proceed until the temperature and relative humidity is changed to the required norm.
3. Cleaning at shutdown (e.g., end of day cleaning), or during batch changeover of same product (of ascending potency)
· Use a vacuum cleaner or lint free cloth to remove loosely stuck powder.
· Dismantle the machine parts and remove them in sequence:
1. Agitator dome
2. Chopper blade
3. Stainless steel bolt
· Use a lint free cloth or vacuum cleaner to clean the dismantled parts.
· Clean the machine and disassemble the parts with lint free cloth.
· Clean the processing area as per the SOP.
· Assemble the parts once cleaned.
· Affix “cleaned” label to equipment.
· Document the cleaning details in the BMR log.
4. Cleaning at Product Changeover (same product of descending potency) – Preventative Maintenance of Contact Parts
· Clean the mixer and the assembly surface using a moist duster followed by a dry clean duster.
· Fill the bowl with 1/3 of its capacity with water, close the lid and run the mixer and chopper for 5 minutes.
· Collect the washing water e.g., by placing a stainless steel drum under the discharge port.
· Open the top lid, remove the agitator blade, and dome by loosening the locking nuts.
· Dismantle the chopper blade by loosening the belt and then remove the blade and washer.
· Transfer the agitator blade and chopper to the washing area, clean both items under a jet of water, and scrub using a clean nylon brush.
· Scrub sticky powder with nylon brush and wash the bowl thoroughly to remove any visible sign of material. .
· Check the underside of the chopper blade, dome and chopper crevices, discharge ports and locking nuts to make sure that the equipment is visibly clean.
· Rinse the machine and the parts with purified water. Send a sample of the rinse water to QA to confirm that it is free from materials from the previous batch.
· Place the “cleaned” label on the machine.
· Document the cleaning details in the BMR log.